本文简要介绍了大型锻造支撑辊全盘管静态感应加热技术、大型钢管内扫描感应加热技术、热轧钢板边缘加热技术的发展历程和主要难点。对感应加热过程中的三个研究课题——末端效应及其对策、加热温度的精确控制和复杂工况下的电磁场分析进行了探索和讨论。
1、托辊全线圈静电感应加热技术
全线圈静态感应加热技术被开发用于支撑辊的感应淬火,其中多匝电磁感应线圈在加热过程中覆盖加热的支撑辊的所有工作表面。辊子旋转以提高圆周温度均匀性,同时在轴向上相对于感应线圈保持相对静止。与传统热处理技术相比,全线圈静电感应加热技术在用于支承辊热处理时具有更深的硬化层和更大的硬度值。通过这项技术,可以提高处理过的滚筒的耐磨性和使用寿命,降低生产和维护成本。由于支撑辊通常直径大于1.5米,高度大于2米,它不可避免地需要比传统感应加热更长的热处理时间。此外,整个辊表面的温度分布差异被限制在±10°C以内。这些要求使得该技术的工业应用难以实现,除非我们能够精确计算感应加热系统参数并控制加热过程。
本研究将支撑辊从450°C加热到900°C以上,在加热过程中物理性能发生较大变化,导致加热系统负荷出现显着波动。这种现象使得难以精确控制加热过程。等效电感随着温度的升高而下降,最终达到一个稳定值。此外,初始电感几乎是高温时的两倍,这使得在负载电容保持恒定的情况下,在整个加热过程中加热频率增加了近50%。这种现象不仅对感应加热系统的稳定运行有很大影响,而且对温度分布也有重要影响。由于感应加热层的厚度要求在100mm以上,加热频率通常在100Hz以下。另一方面,感应系统的参数随着支承辊及其相应加热线圈的尺寸而变化,这使得感应系统参数的设计和加热过程的控制更加复杂。
关于温度分布,在半径方向上比较容易得到理想的温度分布。然而,在加热过程中使用螺线管式感应线圈时不可避免地会出现端部效应,这使得辊表面温度难以控制。沿轴向的辊表面温度随时间呈现不同的非线性分布特征,这主要取决于线圈结构、辊高度和线圈与辊间距。当轧辊表面温度低于居里温度时,轧辊端部温度远低于中部温度。但是,当感应加热过程中辊表面温度超过居里温度时,辊子端部的温度会迅速上升并超过其他部分的温度。这意味着简单地改变感应加热参数并不能提高温度分布的均匀性。为了解决这个问题,已经提出并实施了一种有效的方法,即根据相应加热辊部件的表面温度分别调整加热线圈电流。
对于前面提到的障碍,计算机模拟用于准确模拟感应加热过程和温度分布。首先通过实验结果对仿真模型进行验证和优化。轧辊表层的温度均匀性得到了很好的控制,而轧辊内部保持在较低的温度。红外测温结果表明,整个轧辊表面温差小于±5℃,其中S1 ~S5为红外辐射温度计在感应加热过程最后阶段辊面不同位置测得的温度曲线。这五条曲线几乎相互重叠,这意味着在整个辊表面获得了非常均匀的温度分布。
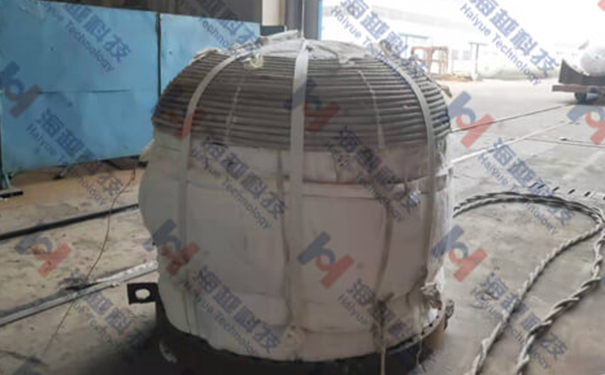
耐磨性是钢管用于物料输送时的关键性能指标之一,直接影响其使用寿命和性价比。在钢管生产过程中,利用热处理技术提高其硬度和耐磨性是一种有效的方法,在工业生产线上有着广泛的应用。但是,对于用于运输的大口径钢管,采用传统的热处理方法存在很多困难。将扫描感应淬火技术应用于钢管内表面,以提高其内部硬度和耐磨性。通过开展成分研究、计算机模拟、物理实验、测温、硬度测试等一系列研究工作,
为提高其使用寿命,钢管最好对其壁厚的50%以上进行感应淬火。由于过热会导致晶粒粗化,因此在加热过程中控制最高温度低于一定温度很重要。这个峰值温度可以通过加热功率、加热频率和钢管的移动速度来控制。为了精确控制整个加热过程,已经实施了计算机模拟。在低移动速度下,热传导占主导地位,这使得温度梯度难以获得。加热过程中内表面温度有一个峰值,而沿半径方向的温差很快就在加热线圈外变得平缓,其中在开始淬火位置内外表面的温差仅在20度以内。因此,为了提高温度梯度,应提高钢管的移动速度。
进行了感应淬火实验,研究了真实加热过程和处理后钢管的力学性能。感应淬火过程中钢管不同位置的热电偶测得的温度与计算结果吻合良好。在钢管圆周方向上温度分布均匀的高温环,该环在整个感应淬火过程中以恒定速度和稳定的温度分布移动,确保在合适的钢成分下,10mm厚的钢管具有1,400 MPa的强度。
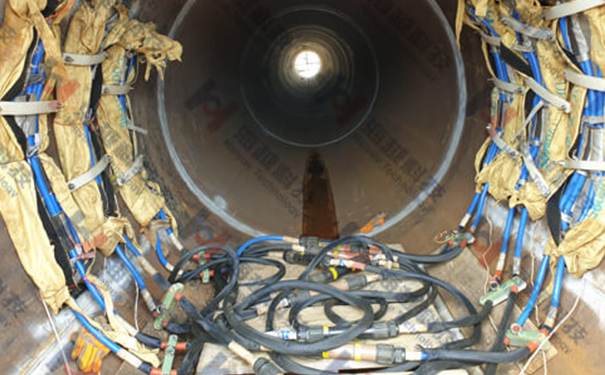
具有“C”形连接芯的边缘加热器用于热轧钢板的感应加热。边缘加热器在应用过程中,经常发生火花现象,这是由输送辊和加热钢板之间的放电电弧引起的。为了避免这种情况,可以采取一些预防措施,例如保持输送机滚筒与地面绝缘,制造直径不等的滚筒,输入相反方向的附近线圈电流等。由于生产线条件恶劣,铁屑和水雾会破坏滚筒的绝缘等级。很难长期保持高绝缘值,这给稳定生产和维护带来了更大的挑战。
分析表明,引起火花现象的主要因素有:(1)滚筒表面粗糙度,(2)输送滚筒的绝缘值,(3)输送滚筒接触部位感应涡流的大小。和钢板。滚筒的表面粗糙度和绝缘值基本上取决于输送滚筒的现场维护,而感应涡流受许多因素的影响,如移动过程中钢板的偏差、钢板的宽度、线圈的相对位置、加热功率等。很明显,如果输送机滚筒与钢板接触位置处的感应涡流较小,则钢板与滚筒之间不太可能发生火花。在这项研究中,通过数值模拟分析了前面提到的影响感应涡流的因素。通过实验结果对数值模拟模型进行了验证和优化,以提高其精度。
发现不同钢板宽度沿辊对板接触线的电流密度分布存在显着差异。窄钢板接触线处的最大涡流密度大于宽钢板。
另一方面,通常有四个线圈并联在钢板的两侧。在加热过程中,钢板很容易向一侧移动,从而导致感应加热电源系统的负载匹配不平衡。在相同的输入电流下,钢板覆盖线圈较多的一侧的感应电流大于另一侧的感应电流。这个结果表明产生火花的可能性,当钢板偏离感应线圈的一侧时会大大增加。而且,前面提到的负载匹配不平衡进一步加剧了线圈中输入电流的不均匀分布,导致钢板中的感应电流有很大的偏差。因此,钢板会在钢板的每一侧被加热到不同的温度,导致沿钢板宽度的物理性能不均匀。因此,强烈建议采取有效措施避免钢板偏斜,以减少火花现象。
以上是关于大型锻造支撑辊全盘管静态感应加热技术、大型钢管内扫描感应加热技术、热轧钢板边缘加热技术的发展历程和主要难点的介绍。更多关于感应加热技术的相关技术知识,请咨询青岛JN江南机电--中频高频电磁感应加热设备制造商。